Surface treatment
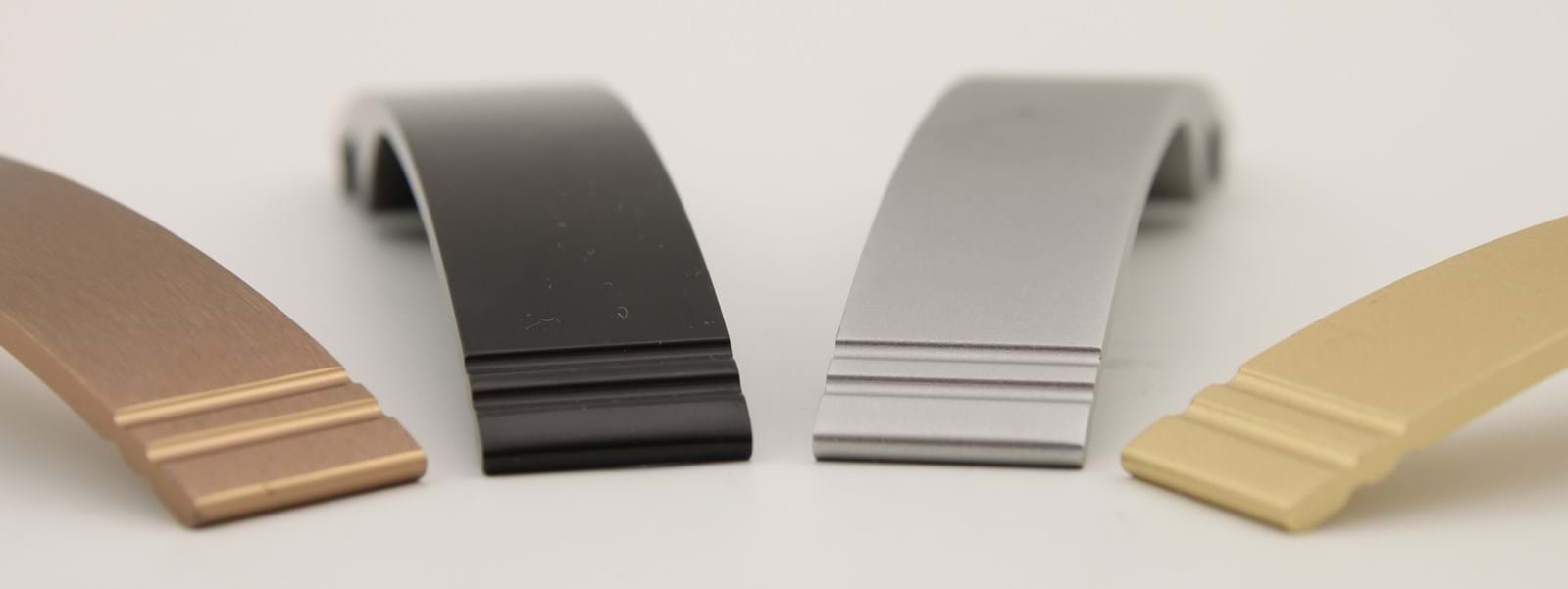
Although aluminium forms a natural oxide layer as protection against corrosion and environmental influences, there can be aesthetic or practical reasons to choose an anodised or painted material.
The most common methods for surface treatment are anodising or painting, both of which serve aesthetic and practical purposes.
Depending on the alloy and the purpose of the surface treatment, there are many ways to achieve the desired result. We are happy to advise you on the best solution for your project.
Mechanical surface treatment
Mechanical surface treatment is a method to ensure a uniform and smooth aluminium surface or to prepare the surface for anodising or painting.
The most common types of mechanical surface treatment are:
- Blasting
- Brushing
- Grinding
- Polishing
Anodising
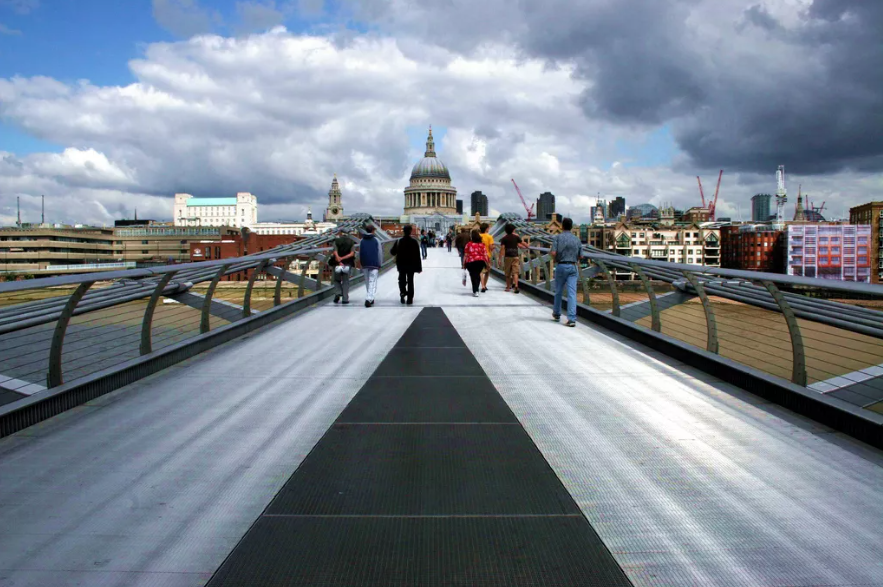
Anodising is a method to strengthen the natural oxide layer. A current is passed through the material while it is immersed in an acid bath, which causes the aluminium to react and form a thicker protective layer.
In other words, anodising is a chemical transformation of the surface. The material is still 100 % aluminium (except for any added alloying elements).
The process is highly controlled, which is part of the reason for its widespread use. An anodised aluminium surface has a metallic look just like the raw surface, but it appears more uniform.
A stable surface over time
Over time, a raw plate will oxidise and develop a dull and aesthetically uneven surface, but an anodised plate will retain the chosen surface finish over time.
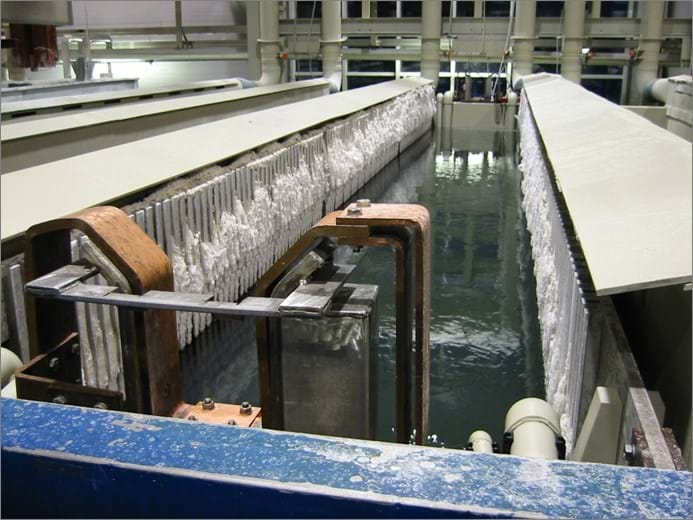
All alloys can be anodised, but the aesthetic result is not the same for all alloys. If the purpose of anodising is to achieve a uniform surface, we recommend alloys EN AW-5005 AQ (sheets) and EN AW-6060/ EN AW-6063 (profiles).
The colour of the anodised surface, including natural anodising, depends on the alloy and the quality of the surface. This means that the result of the anodising can differ from supplier to supplier because the material may be different variants of the same alloy within the standard.
This image shows different alloys with the exact same anodising:
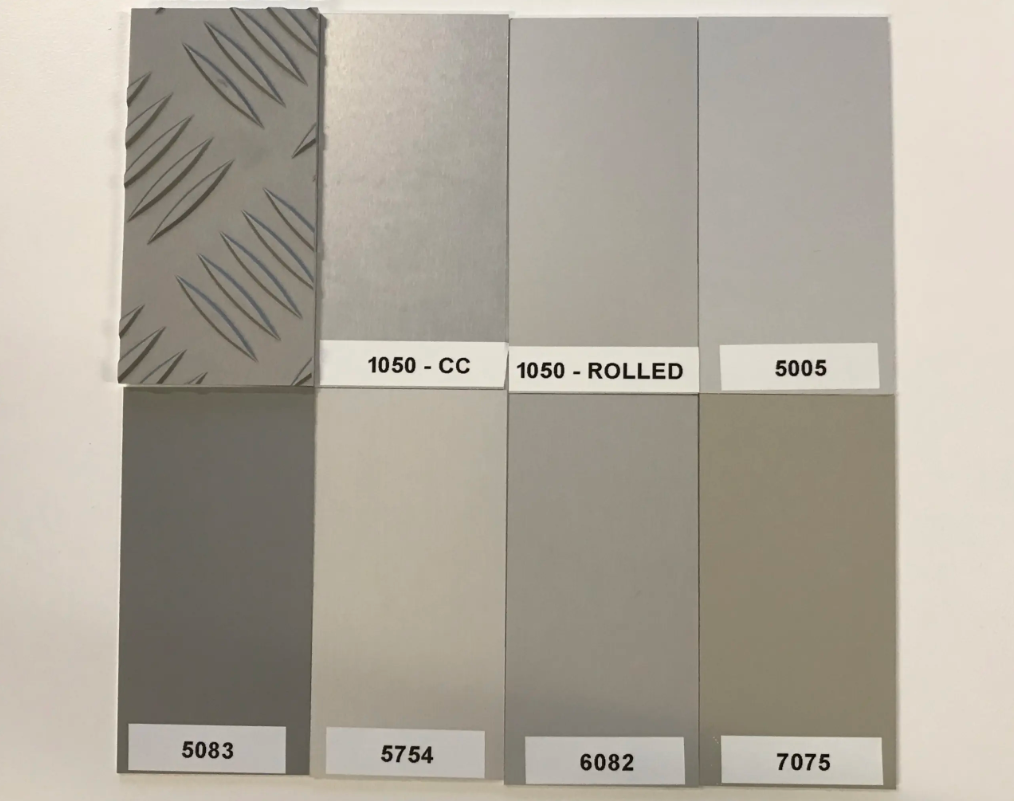
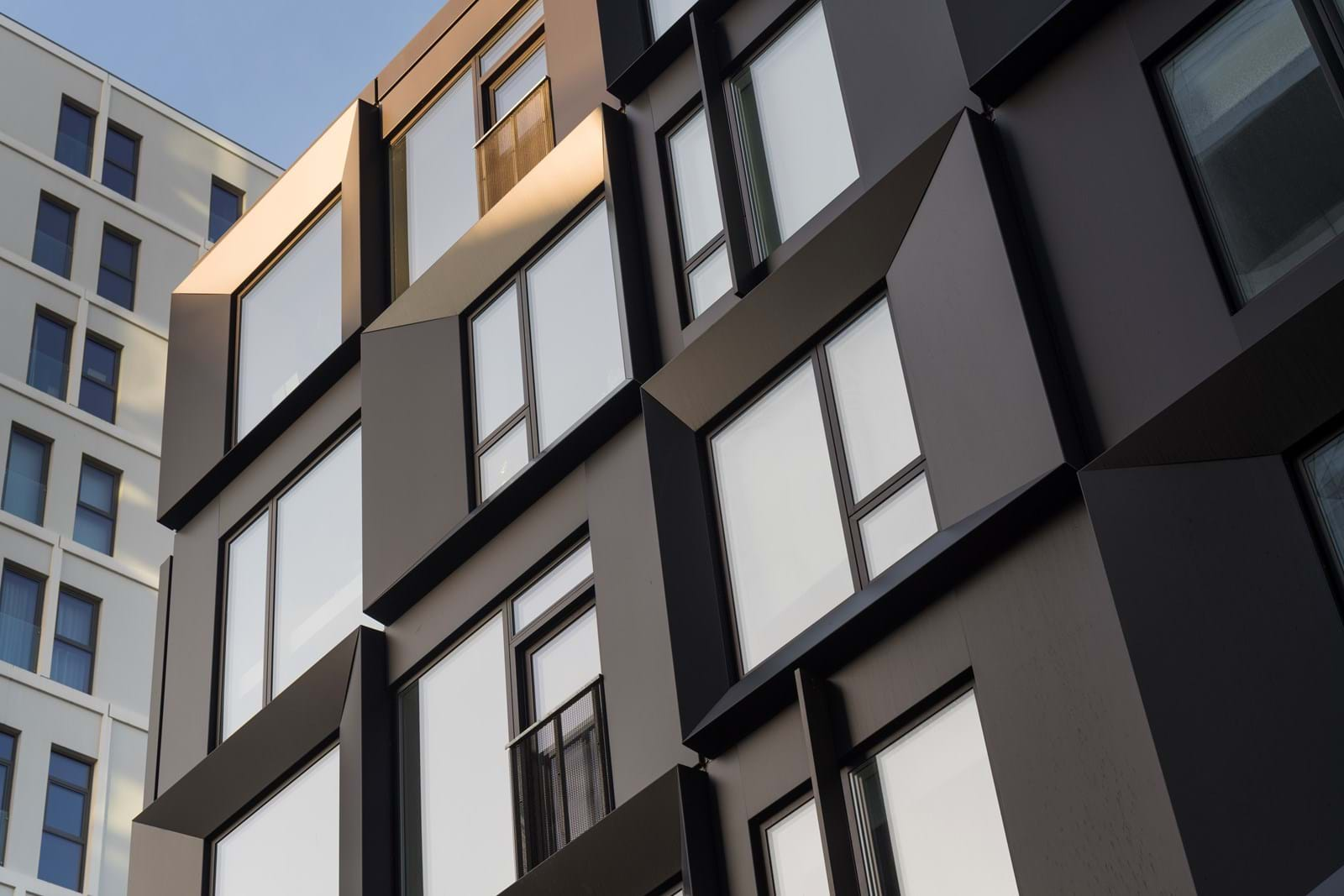
The standard anodising method is natural (clear) anodising, but there is a wide range of options to dye the anodising. Whether natural or coloured, anodising is always partially transparent.
Anodising and machining
The machining options depend on how the material is anodised.
In case of batch anodising, we recommend machining before anodising. This way you avoid damaging anodised areas while machining.
Anodised sheets from our standard range are generally coil anodised and can usually be bent after anodising without any issues.
Anodising thickness
It is important to consider the thickness of the anodising. The thickness affects both the aesthetic result and the level of corrosion protection.
For most purposes, an anodising thickness of 10-15 µm is sufficient. We generally recommend 10 µm for purely aesthetic purposes and 15 µm for durability, e.g. facades.
We recommend that you consult your sales representative about the right thickness for your specific project and environment.
It is important to consider the surroundings and environment even though the material is anodised.
For example, regardless of thickness, anodising does not protect against galvanic corrosion. Galvanic corrosion occurs when the aluminium comes into direct contact with a more noble metal through an electrolyte – often in an environment where salt water is present, such as marine environments.
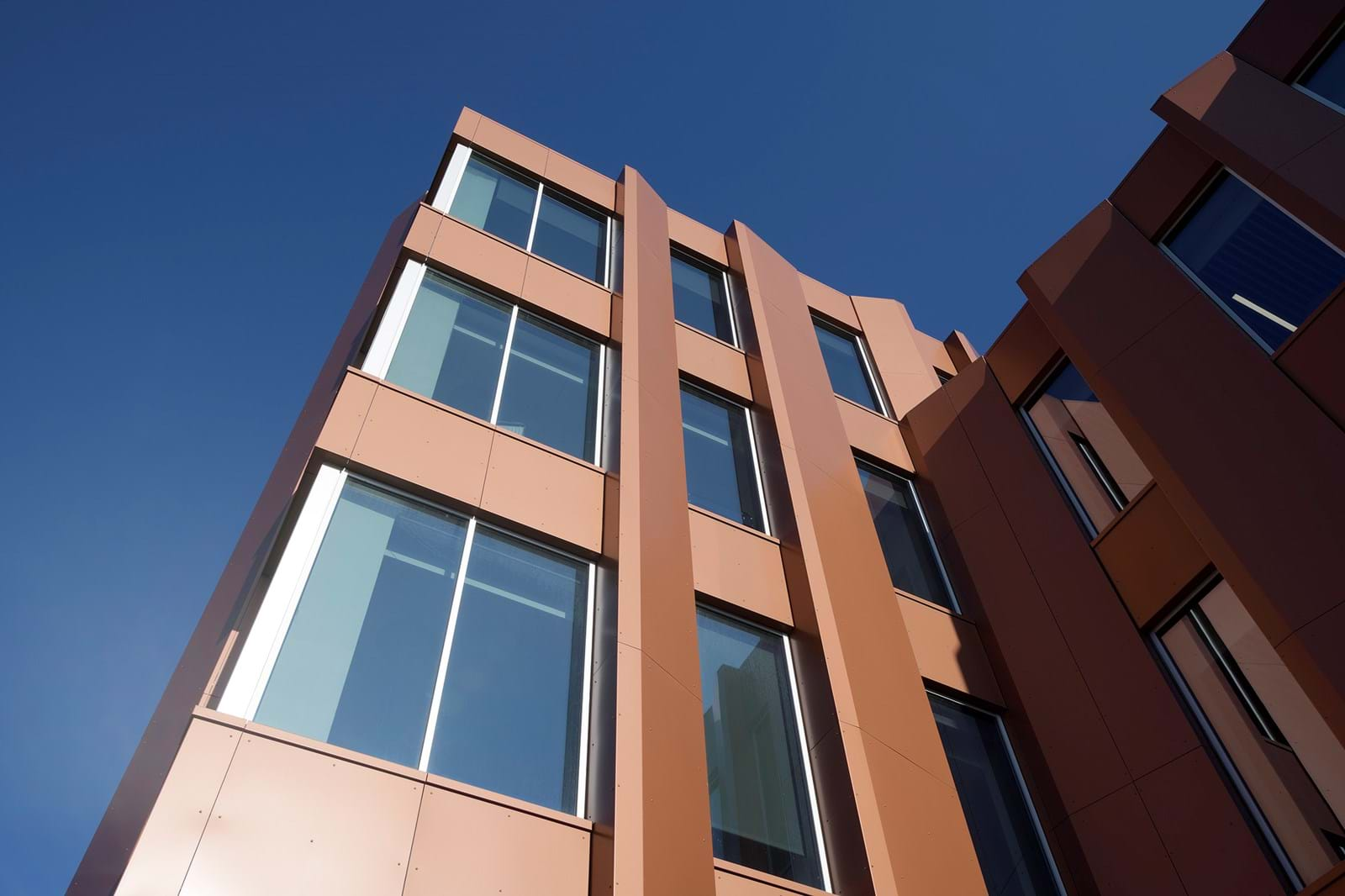
Aluminium can be painted in all RAL and NCS colours and with a wide range of textured and metallic paints.
Profiles are usually powder coated, while the sheets in our range are generally painted with a standard polyester liquid paint.
Painting and machining
The machining options depend on how the material is coated.
As a rule of thumb, we recommend that the material is machined before painting. This eliminates the risk of uncoated areas from cutting or chipping.
Painted plates from our standard range are usually coated with liquid paint and can be bent after painting.
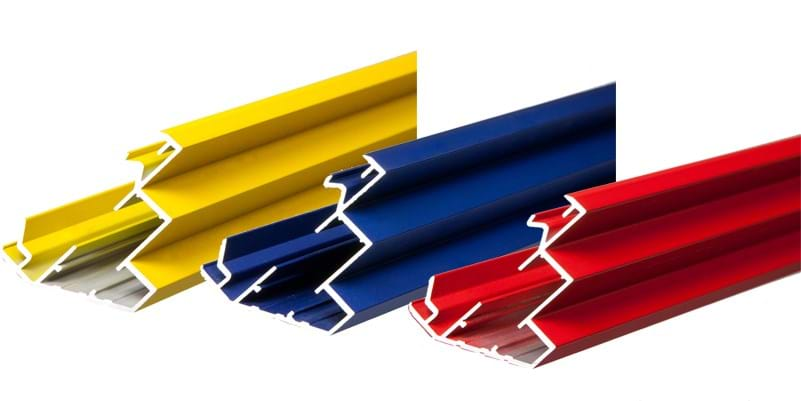
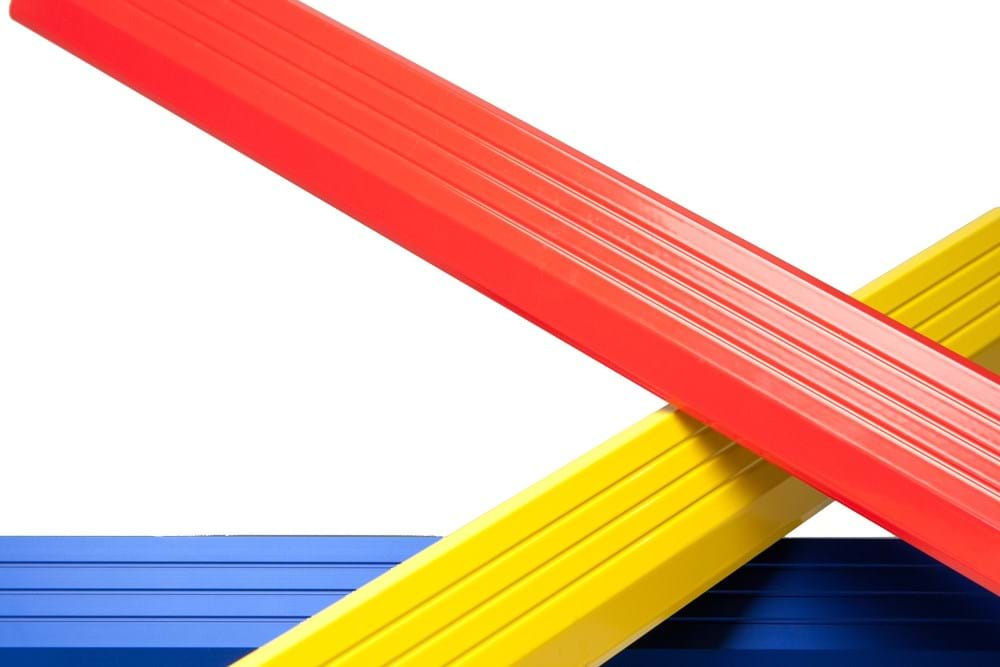